5 Ways Welting Works
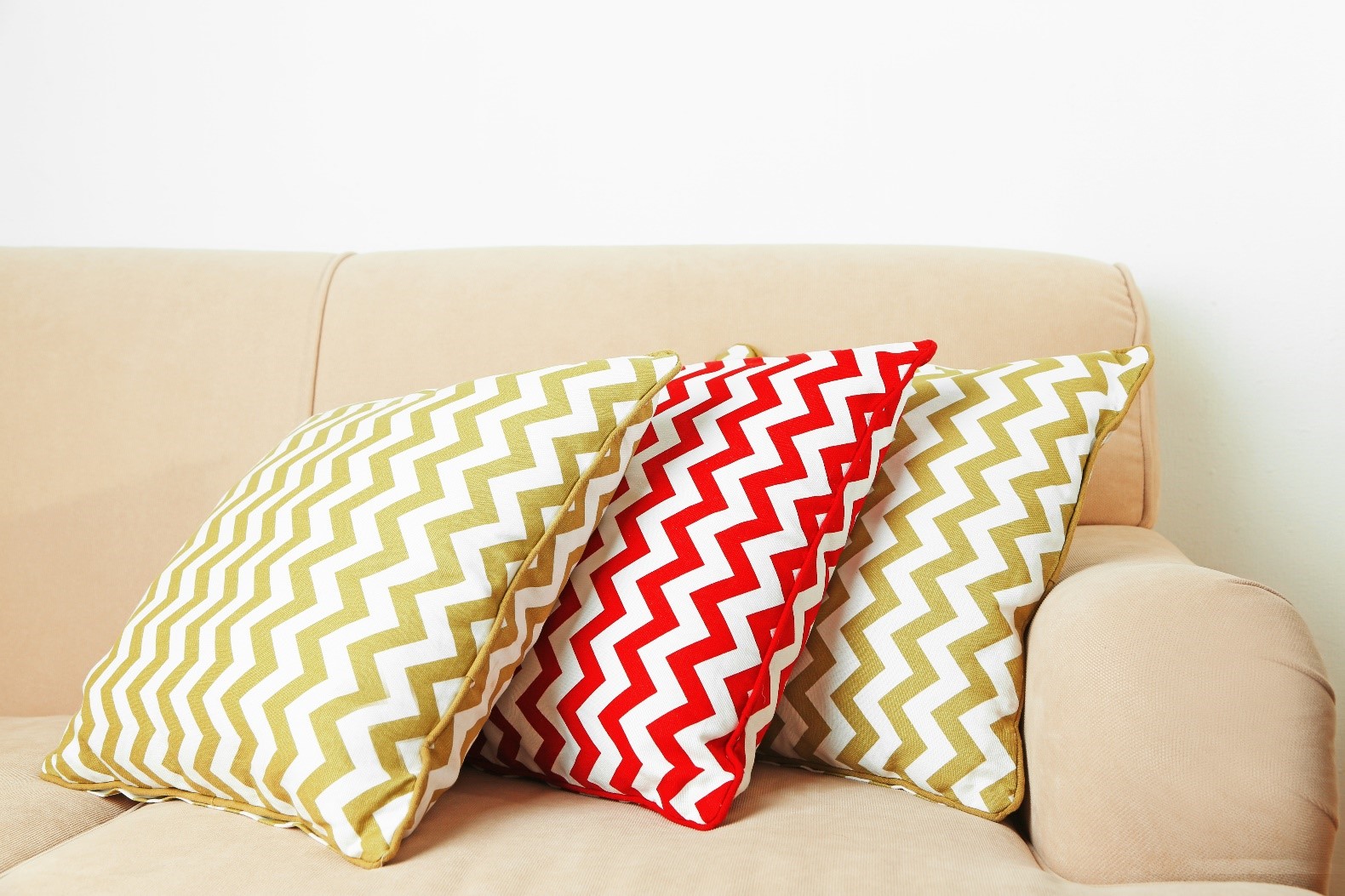
Welding, a fundamental process in various industries, including construction, manufacturing, and repair, involves joining two metal pieces together by applying heat, pressure, or both, with or without filler metal. There are several welding techniques, each with its unique characteristics, applications, and requirements. Here, we’ll delve into five significant ways welding works, exploring their processes, benefits, and typical uses.
1. Shielded Metal Arc Welding (SMAW)
Shielded Metal Arc Welding, also known as “stick” welding, is one of the most common and versatile welding processes. It uses a consumable electrode covered in flux to protect the arc from atmospheric gases. The flux also helps in removing impurities and improving the quality of the weld. This method is widely used for maintenance and repair work due to its simplicity and the ability to weld thick metals. It’s effective in outdoor environments because the flux protects the arc, making it less susceptible to wind interference.
How it Works: - The welder holds an electrode holder in one hand and a shield (if needed) in the other. - The electrode is struck against the workpiece to create an arc. - The welder manipulates the electrode to maintain the arc length and controlled heat input. - The flux covering the electrode melts and forms a shield of gas and slag, protecting the weld area.
2. Gas Metal Arc Welding (GMAW)
Known as MIG (Metal Inert Gas) welding, this process uses a continuous wire feed as the electrode and an inert gas to shield the arc. GMAW is highly versatile, suitable for welding a variety of metals, including steel, aluminum, and stainless steel. It offers high speed and low operator skill requirements compared to SMAW, making it highly efficient for production environments.
How it Works: - The welder uses a gun connected to a spool of wire and a gas supply. - Depressing the gun’s trigger releases the wire and starts the gas flow. - The welder maintains the arc by moving the gun along the seam to be welded. - The inert gas (like argon or helium) protects the weld from atmospheric gases.
3. Gas Tungsten Arc Welding (GTAW)
Also known as TIG (Tungsten Inert Gas) welding, GTAW uses a non-consumable tungsten electrode to produce the weld. The weld area is protected from atmospheric gases by an inert gas shield. This process is renowned for its high-quality welds, especially on thinner materials and where appearance matters. It requires a high level of skill and is typically used for critical welds, precision work, and in industries like aerospace and automotive.
How it Works: - The welder holds a torch with a tungsten electrode and a foot or finger pedal to control the current. - The gas nozzle around the electrode emits inert gas to shield the weld area. - Filler metal is manually added into the weld pool, allowing for precise control over the weld. - The welder carefully controls the arc and moves the torch to create the weld.
4. Flux Cored Arc Welding (FCAW)
This process combines the benefits of SMAW and GMAW, using a special electrode that is similar to the wire used in GMAW but is covered in flux. FCAW can be used with or without shielding gas, offering flexibility and high weld quality. It’s particularly useful in construction and fabrication due to its ability to weld through mill scale and its tolerance to less-than-ideal conditions.
How it Works: - The equipment is similar to GMAW but with a special flux-cored wire. - The flux in the wire generates a shielding gas when melted, protecting the weld. - The welder has the option to use an additional shielding gas for extra protection. - It offers faster deposition rates and better penetration than GMAW, making it suitable for thicker materials.
5. Submerged Arc Welding (SAW)
Submerged Arc Welding involves the use of an electric arc to melt and join metals, but unlike other forms, the arc is submerged under a layer of flux. This process is known for its high deposition rates, making it efficient for welding long seams or thick materials, especially in steel mills and shipbuilding.
How it Works: - The weld area is covered with a layer of flux. - An electric arc is struck between the workpiece and a consumable electrode, which is buried under the flux layer. - The arc melts the electrode, the base metal, and the flux, creating a weld. - The flux protects the weld from atmospheric gases, eliminates spatter, and can improve the weld’s mechanical properties.
Each welding technique has its unique advantages and is suited for specific applications. Understanding the different ways welding works is crucial for selecting the appropriate method for a project, ensuring high-quality results, efficiency, and safety. Whether it’s the precision of GTAW, the versatility of GMAW, or the efficiency of SAW, each process contributes to the diverse and ever-evolving field of welding.
What is the most versatile welding process?
+Gas Metal Arc Welding (GMAW) is often considered the most versatile due to its ability to weld a variety of metals and its wide range of applications, from thin sheet metal to thicker plates.
Which welding process is known for high-quality welds?
+Gas Tungsten Arc Welding (GTAW) is renowned for producing high-quality welds, particularly in precision work, and is often used in industries where appearance and strength are critical, such as aerospace and automotive.
What is the role of flux in welding processes?
+Flux in welding helps in several ways: it shields the weld area from atmospheric gases, removes impurities, and can improve the weld’s mechanical properties. In processes like Shielded Metal Arc Welding (SMAW) and Flux Cored Arc Welding (FCAW), flux plays a critical role in the quality of the weld.
Which welding process offers high deposition rates and is suitable for thick materials?
+Submerged Arc Welding (SAW) is known for its high deposition rates, making it particularly efficient for welding long seams or thick materials, and is often used in applications such as shipbuilding and steel mills.
What factors should be considered when choosing a welding process?
+Several factors should be considered, including the type and thickness of the material to be welded, the desired weld quality, the production efficiency required, the skill level of the welder, and the specific application or industry standards.