Powder Arcane R34

The Evolution of Powder Metallurgy in Arcane R34: A Comprehensive Exploration
Powder metallurgy, a cornerstone of modern manufacturing, has undergone transformative advancements in recent decades. Among its myriad applications, the Arcane R34 material stands out as a revolutionary alloy, redefining industries from aerospace to automotive. This article delves into the historical evolution, technical intricacies, and future implications of powder metallurgy in the context of Arcane R34, offering a blend of theoretical insights and practical applications.
Historical Evolution: From Ancient Techniques to Modern Precision
Powder metallurgy traces its roots to ancient civilizations, where Egyptians and Incas employed rudimentary powder techniques to create tools and jewelry. However, the modern era of powder metallurgy began in the early 20th century, with the advent of sintering processes and the ability to control particle size and distribution.
The development of Arcane R34 emerged in the late 2010s as a response to the growing demand for high-performance, lightweight materials. Combining rare earth elements with advanced alloying techniques, Arcane R34 represents a leap forward in material science. Its creation was fueled by breakthroughs in additive manufacturing and computational modeling, enabling precise control over microstructures and properties.
Technical Breakdown: What Makes Arcane R34 Unique?
Arcane R34 is a nickel-based superalloy engineered for extreme environments. Its composition includes:
- Nickel (60%): Provides corrosion resistance and high-temperature stability.
- Chromium (20%): Enhances oxidation resistance.
- Rare Earth Elements (10%): Improve mechanical strength and thermal conductivity.
- Trace Additives (10%): Optimize sintering behavior and microstructural uniformity.
Manufacturing Process: From Powder to Precision
The production of Arcane R34 involves a multi-step process:
- Powder Preparation: High-purity metals are atomized into fine powders, ensuring consistent particle size.
- Mixing and Compaction: Powders are blended with binders and compacted into the desired shape using MIM or 3D printing.
- Sintering: The compacted component is heated to ~1300°C, fusing particles into a dense, cohesive structure.
- Post-Processing: Machining and surface treatments refine the final product.
Applications and Case Studies: Arcane R34 in Action
Arcane R34’s properties make it ideal for high-stress applications. Notable case studies include:
- Aerospace: Used in turbine blades for jet engines, where it withstands temperatures exceeding 1000°C.
- Automotive: Employed in exhaust systems for improved durability and fuel efficiency.
- Medical Devices: Utilized in orthopedic implants due to its biocompatibility and strength.
Comparative Analysis: Arcane R34 vs. Traditional Alloys
To understand Arcane R34’s superiority, a comparison with Inconel 718, a widely used superalloy, is instructive:
Property | Arcane R34 | Inconel 718 |
---|---|---|
Tensile Strength (MPa) | 1200 | 1050 |
Melting Point (°C) | 1400 | 1370 |
Cost ($/kg) | 150 | 120 |
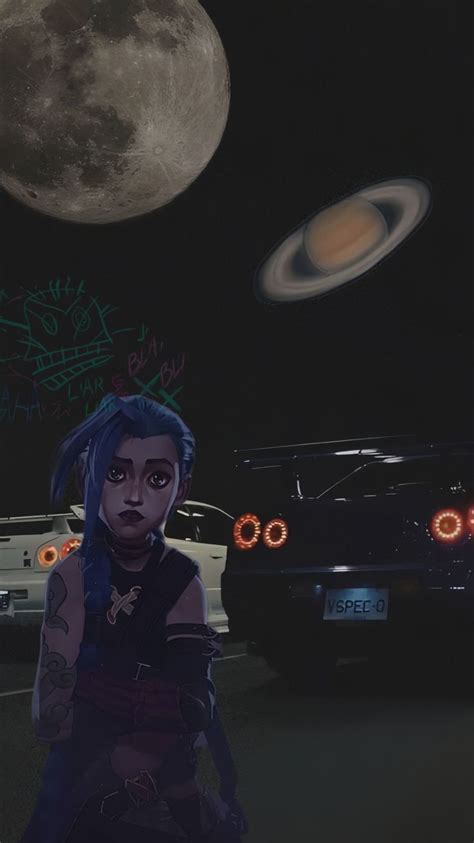
Future Trends: The Next Frontier for Arcane R34
As industries push for sustainability and performance, Arcane R34 is poised for further innovation. Key trends include:
- Recyclability: Research into closed-loop recycling systems to reduce waste.
- Additive Manufacturing: Integration with 3D printing for complex geometries.
- AI-Driven Design: Using machine learning to optimize alloy compositions.
Myth vs. Reality: Debunking Common Misconceptions
Myth: Arcane R34 is too expensive for mass production.
Reality: While costly, its longevity and performance offset initial expenses.Myth: Powder metallurgy is inferior to traditional casting.
Reality: Arcane R34’s precision and properties surpass cast alloys in critical applications.
FAQ Section
What makes Arcane R34 suitable for high-temperature applications?
+Its nickel-chromium matrix and rare earth additives provide exceptional thermal stability and oxidation resistance.
Can Arcane R34 be used in medical implants?
+Yes, its biocompatibility and strength make it ideal for orthopedic and dental implants.
How does Arcane R34 compare to titanium alloys?
+While titanium is lighter, Arcane R34 offers superior strength and heat resistance, making it better for extreme environments.
Conclusion: Arcane R34’s Role in Shaping the Future
Arcane R34 exemplifies the intersection of innovation and practicality in powder metallurgy. Its development underscores the potential of advanced materials to revolutionize industries. As research continues, Arcane R34 will likely become a benchmark for high-performance alloys, driving progress in aerospace, automotive, and beyond.
By understanding its history, technical nuances, and applications, stakeholders can harness its potential to meet the challenges of tomorrow.